How Can Artificial Intelligence Be Used for Measuring Aerodynamic Flows?
•5 min read
- Languages, frameworks, tools, and trends
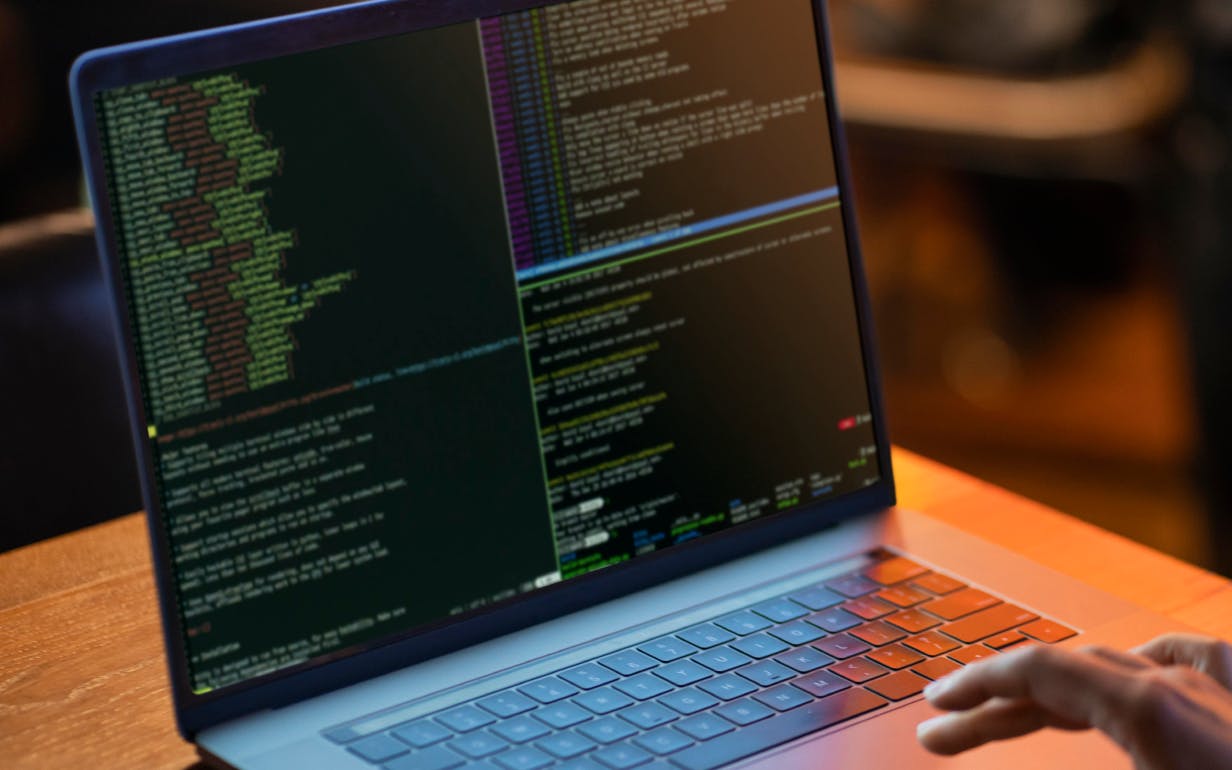
What if we could create a car with adjustable aerodynamics? What if we had a real-time monitoring system that could be adjusted to any aerodynamic flow condition? This is where artificial intelligence (AI) may significantly impact the traditional design process.
Aerodynamics plays a big role in how much power road vehicles use. As a result, a special aero package may considerably increase the range of future electric vehicles, contributing to the fossil-fuel independence we all desire.
Computational fluid dynamics (CFD) and wind tunnel tests optimize vehicle aerodynamic performance. In most cases, a flow condition is specified, a collection of configurations is tried, and the best solution is chosen. Unfortunately, this type of approach frequently results in a sub-optimal configuration, in which neither are all the parameters considered nor is the chosen configuration the best for various flow circumstances.
Therefore, it is conceivable to develop an adaptive, closed-loop control that can independently optimize vehicle aerodynamics for any external flow situation by combining AI with wind tunnel experiments (WTEs).
NEXTFLOW: Developing tech to monitor turbulent flows
The major goal of the NEXTFLOW research project at the Universidad Carlos III de Madrid (UC3M), which is financed by an ERC Starting Grant from the European Union, is to develop new technologies that are more efficient and trustworthy in order to monitor turbulent flows.
These techniques, which take advantage of recent advances in artificial intelligence and data mining, can help enhance the aerodynamics of vehicles and lessen their environmental impact.
Improved approaches for characterizing and managing the behavior of turbulent flows are one of the main issues in aerodynamics (the fluid motion that occurs around an airplane wing, for example).
"They are chaotic, with complicated dynamics, making it challenging to comprehend their behavior using the available approaches fully," says Stefano Discetti from UC3M's Department of Bioengineering and Aerospace Engineering, the NEXTFLOW project coordinator.
Due to turbulence's crucial role in many industrial applications, optimizing ways to quantify turbulent flows is a significant feature in today's business. Obtaining more exact knowledge of its dynamics would allow us to use it in real-world scenarios, such as the transportation industry.
Turbulent flows affect the forces opposing the movement of many sorts of vehicles, including automobiles, airplanes, and ships, according to experts. Thus, a better understanding of them can enhance their performance and lessen their environmental effect.
According to Discetti, current methodologies for detecting turbulent flow in experiments only offer "a partial description of their velocity, temperature, or pressure”. This new ERC project aims to build a new generation of measurement instruments using artificial intelligence and data mining techniques so that a more thorough description of their dynamic behavior can be acquired and more information obtained on how to regulate them.
Using AI to enhance accuracy of particle image velocimetry (PIV)
Volumetric particle image velocimetry is one of the approaches being employed. It allows for a 3D reconstruction of fluid flow following the motion of particles visible by laser light.
Scientists intend to use data from high sampling-frequency point probes to supplement the 3D description with temporal dynamics as part of this research. Furthermore, AI-based methods will be developed to increase the accuracy of the particle image velocimetry methodology. The UC3M researchers offered a unique strategy based on data mining to achieve this aim in a recent paper published in the Experimental Thermal and Fluid Science journal.
By using fundamental fluid mechanics equations, high-precision and time-resolved observations will be used to produce pressure fields. The researchers want to utilize this to construct compact models that may be used to explain flow behavior and develop control logic properly.
"These findings could lead to new tools that bridge the gap between laboratory experiments and the characterization and control of flows in real-world applications," says Discetti. This could improve processes and reduce the environmental impact of various industry sectors, particularly the aeronautical industry.
Applications of AI in various areas of aerodynamics
- AI can assist in computational aerodynamics.
- It can assist in the aerodynamic design and development process.
- It can be used to design aerodynamic bikes.
- It can be used to acquire new knowledge.
- It can leverage available information to minimize the time necessary for numerical solutions to tractable aeronautical design and development issues.
Figure 1: Artificial intelligence assists computational aerodynamics in aerodynamic design and development.
Image source: Author
CNNs’ potential to influence design processes
Deep learning offers a quick alternative option as an efficient function approximation approach in high-dimensional domains. Moreover, deep learning architectures like deep neural networks (DNNs), commonly employed in data mining, are well-suited for extracting multi-scale characteristics from large, high-dimensional datasets.
Deep convolutional neural networks (CNNs) are often used to analyze visual images. Previous research (Lecun et al., 1998; Taylor et al., 2010; Zuo et al., 2015) has shown that CNNs can learn high-level features even when the input is highly correlated spatially and temporally.
The growing interest in CNNs in fluid mechanics stems partly from their potential benefits of form representation flexibility and scalability for 3D and transient situations.
Figure 2 (a) Shared-encoder but separated decoder
Figure 2 (b) Shared-encoder and decoder
Image source
Figure 2 (b) Shared-encoder and decoder
Figure 2: A CNN-based network architecture for airfoil shape is used to predict aerodynamic flow fields. Arrows indicate the forward operation directions. The kernel size and number of filters are listed below each operation. Convolutional and deconvolutional layers have one-dimensional strides in each direction. Except for the output layer, each layer is followed by a Swish activation function (Ramachandran et al., 2017).
The research shows that CNNs can enable simulation-based design and optimization near real-time, paving the way for a more efficient design process. It's worth noting that training with only three airfoil shapes is a data limitation that limits general prediction behavior for unknown airfoil geometry from other families.
Future studies will aim to train using a large dataset that includes several airfoil families and enrich the training datasets with operations like translation and rotation to turn a collection of input data into a larger set of significantly changed data (Shijie et al., 2017). This enhancement will prevent the network from learning irrelevant patterns while also significantly improving performance. Exploring physical loss functions can also be useful for directly putting physical limitations on networks, such as mass and momentum conservation.